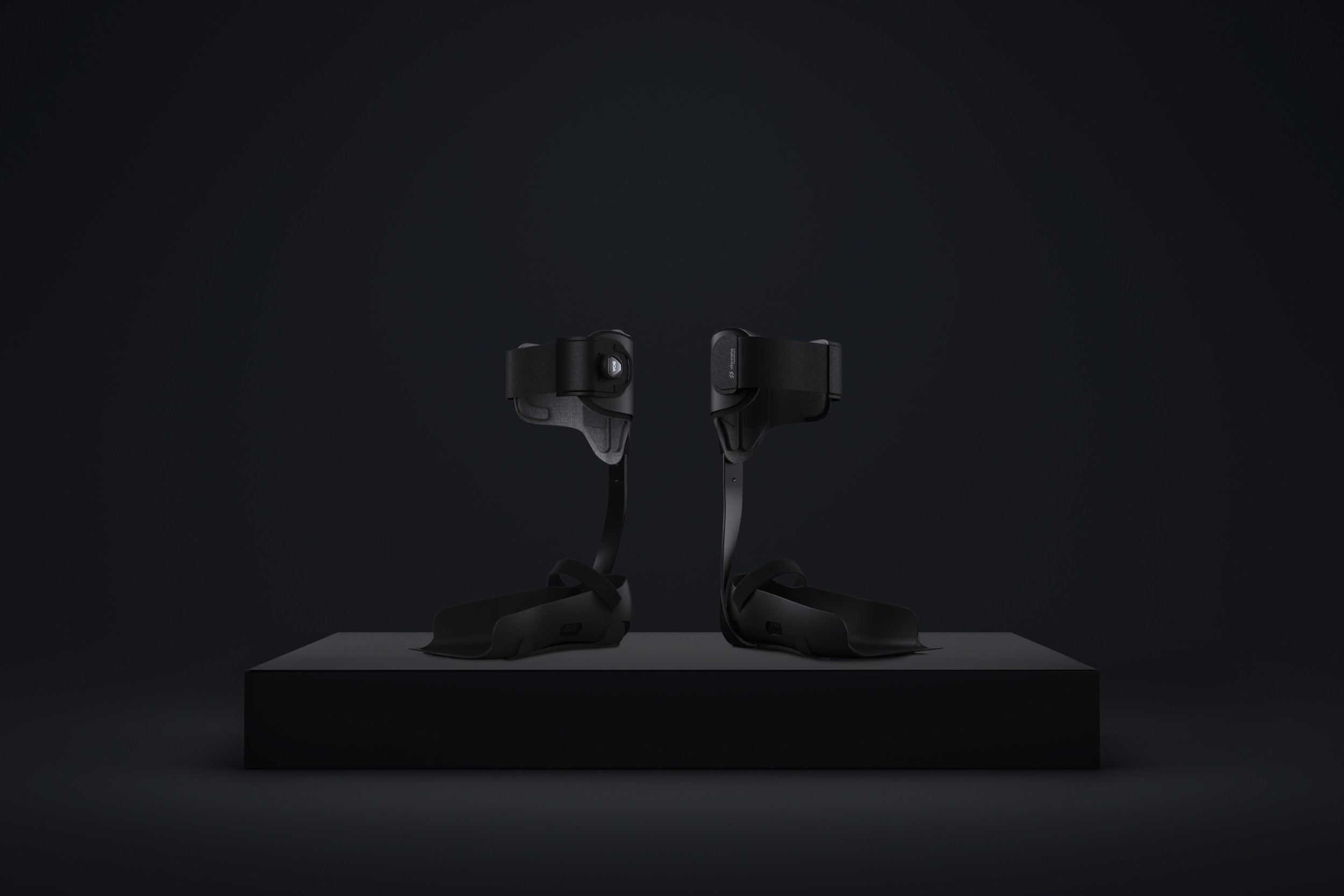
Swift
I led the design of Elevate's innovative product, Swift, from ideation to production. As the lead product designer, I managed the project through all phases, including overseeing engineering execution.
Starting with in-person discovery at clinics, I identified pain points for clinicians and patients using custom ankle foot orthoses (AFO). We set out to design a carbon-fiber brace that could be fabricated in-clinic in under an hour, a huge improvement over competitor products with 3 week lead times and a 15% remake rate.
The innovation lies in both the process (fabrication using just a heat gun and shears) and the product (a dynamic, durable, and premium brace).
Key features:
Carbon fiber strut for durability and natural gait
Heat-moldable plastic components for custom fitting
BOA dial calf strap for micro-adjustments
Premium, comfortable straps
Intuitive packaging that guides clinicians through fabrication
We ran into several challenges making the product moldable and trimmable with just a heat gun and shears, but also look premium after fabrication.
We tested >50 materials before finding one that achieved a perfect balance. We sweat over the details to ensure a premium product — we designed straps that could be inserted into the boot without using Velcro, silicone ‘plugs’ to prevent the slots in the boot from deforming with heat, and included a sanding block to finish the edges. Three similar straps proved very confusing for the user, so we added embossed dots on the boot that match dots on the corresponding straps.
I carefully designed the packaging to intuitively instruct the clinician in the fabrication process:
We built a local user base of ‘Elevate ambassadors’ who I brought in for ongoing user testing from early prototypes to final product.
After months of verification and validation testing, lots of cracked carbon fiber, melted plastic, and painful straps, we were live!
I presented our new product to one of the largest orthopedic clinics and started gathering feedback from customers for continuous and future improvements.
I built out an internal wear testing initiative so every employee wore a prototype brace for 10k steps/day and conducted a series of extreme movements (bending over, lunging, squatting). I integrated a daily survey into Slack to collect the data.
This is me wearing an early prototype through the airport and ship testing a packaging prototype!